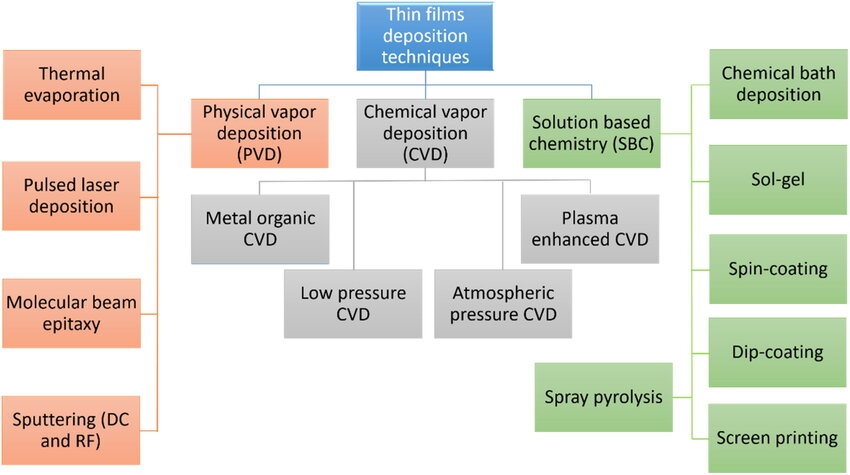
Liquid Crystal Polymer (LCP) Films in the Electronics Industry
1. Introduction
Liquid Crystal Polymer (LCP) is a high-performance polymer with unique characteristics that make it essential for advanced electronic applications. LCP exhibits liquid crystalline behavior when heated or dissolved in solvents, combining fluidity with molecular order. This duality imparts the material with exceptional thermal resistance, dielectric properties, and dimensional stability, positioning it as a superior choice for high-performance applications.
Characterized by its rigid rod-like molecular structure, LCP is known for tight molecular packing and strong intermolecular forces, enabling outstanding flow characteristics, ultra-low water absorption, and high-temperature performance. Since its development in the 1970s, LCP materials have been categorized into three types—Type I, II, and III—each tailored for specific applications across electronics, telecommunications, and industrial manufacturing. Among these materials, LCP films have garnered significant attention for their exceptional stability under high-speed and high-frequency conditions, making them indispensable in advanced electronic packaging and communication systems.
Fig. 1 Principle of Liquid Crystal Display
2. Introduction to LCP Films
2.1 What Are LCP Films?
LCP films are thin, flexible materials made from liquid crystal polymers. When heated or dissolved, LCPs exhibit a liquid crystalline state, combining the fluidity of liquids with the molecular order of crystalline solids. This unique behavior allows LCP films to deliver unmatched thermal resistance, excellent dielectric properties, and superior dimensional stability. Their molecular structure, composed of rigid rod-like chains, results in high mechanical strength, ultra-low water absorption, and exceptional stability under extreme conditions. These properties make LCP films highly sought after in high-frequency electronics and advanced communication technologies.
Fig. 2 Molecular Structure of Different States of Matter
2.2 Development History of LCP Films
The history of LCP development reflects decades of innovation, starting in the 1970s and involving contributions from various companies and regions:
- Type I LCP (1972): The first commercial LCP, Ekonol, was introduced in the U.S. It featured a rigid molecular structure and excellent heat resistance, making it ideal for electronic components such as connectors. Japan’s Sumitomo Chemical later advanced the technology, positioning Japan as a key player in LCP production.
- Type II LCP (1984): Hoechst-Celanese introduced Vectra, a simpler and more mechanically robust LCP. Type II materials became globally popular for applications like antenna materials.
- Type III LCP (1976): Eastman Kodak developed a flexible ester-based LCP, branded X-7G. While this type offered lower heat resistance, it found niche applications in sensors and tubing.
Fig. 3 Development History of LCP
2.3 Classification of LCP Films
LCP films are classified based on liquid crystal formation, product grade, and molecular structure.
Liquid Crystal Formation:
- Lyotropic LCPs: Processed in solution, commonly used for fibers and coatings.
- Thermotropic LCPs: Processed in molten states, widely applied in injection molding and film-grade materials.
Product Grades:
- Injection Grade: Suitable for high-precision parts with complex geometries, offering heat resistance and mechanical strength.
- Film Grade: Used in high-performance films for electronic and electrical applications due to their low dielectric constant and stability.
- Fiber Grade: Processed into high-strength fibers for reinforcing composite materials.
Molecular Structure:
- Type I: High heat resistance (250–350°C), used in electronic components.
- Type II: Balanced heat resistance and processing capabilities (180–250°C), ideal for antennas.
- Type III: Lower heat resistance (100–200°C), used in niche applications like sensors.
Types |
Heat Deformation Temperature |
Molecular Structure |
Type I |
250-350℃ |
|
Type II |
180-250℃ |
|
Type III |
100-200℃ |
|
3. Key Properties of LCP Films
3.1 Stable Low Dielectric Constant and Loss
LCP films exhibit low dielectric constants (2.9–3.5) and dielectric losses (0.002–0.004), which are critical for high-speed and high-frequency signal transmission. These properties enable faster electrical signals with minimal distortion, making LCP films ideal for applications like 5G communications and millimeter-wave systems. Even at frequencies above 10 GHz, LCP films maintain excellent performance, reducing signal delays and ensuring data integrity.
Fig 4 LCP Significantly Reduces High-Frequency Transmission Losses
3.2 Low Water Absorption and Thermal Expansion
LCP films have a water absorption rate of less than 0.04%, ensuring stable performance in humid environments. This property prevents increases in dielectric constant or loss, maintaining signal quality under varying conditions. Additionally, their low coefficient of thermal expansion (10–17 ppm/°C) ensures dimensional stability during thermal cycling, critical for precision electronics and flexible circuits.
Fig. 5 Comparison of Transmission Loss Before and After Moisture Absorption Between LCP Substrate and PI Substrate
3.3 High Dimensional Stability and Barrier Properties
The unique molecular structure of LCP films provides exceptional dimensional stability, even under mechanical stress or extreme temperatures. LCP films resist thermal expansion and contraction, making them suitable for heat-sensitive devices and high-frequency circuits. Moreover, their excellent barrier properties protect against gases, moisture, and chemicals, enhancing the reliability of electronic components in harsh environments.
Fig. 6 The Special Molecular Structure of LCP Determines Its Unique and Excellent Performance Compared to Other Thermoplastic Materials
3.4 Outstanding Heat Resistance and Temperature Cycling
LCP films can withstand temperatures above 250°C without degradation, making them ideal for high-temperature applications like automotive electronics and 5G communication equipment. Their ability to resist thermal shock ensures reliability during rapid heating and cooling cycles, critical for aerospace and industrial applications.
3.5 Excellent Mechanical Properties
LCP films offer high tensile strength (150–300 MPa) and modulus (10–25 GPa), ensuring resistance to mechanical stress while remaining lightweight. These properties make them suitable for applications requiring durability and precision, such as flexible printed circuit boards (FPCs), antennas, and aerospace components.
Property |
Values |
Dielectric Constant (Dk) |
2.9 - 3.5 |
Dielectric Loss (Df) |
0.002 - 0.004 |
Water Absorption |
< 0.04% |
Coefficient of Thermal Expansion (CTE) |
10 - 17 ppm/°C |
Operating Temperature Range |
-50°C to over 250°C |
Tensile Strength |
150 - 300 MPa |
Young's Modulus |
10 - 25 GPa |
Key Applications |
High-frequency applications, 5G communications, Flexible circuits, Aerospace |
4. Comparison with Other High-Performance Materials
LCP films are often compared with other high-performance materials like polyimide (PI) and polytetrafluoroethylene (PTFE). While PI excels in heat resistance, its high thermal expansion coefficient can lead to dimensional instability. PTFE offers superior chemical resistance but lacks the mechanical strength and electrical properties of LCP in high-frequency applications. LCP films provide a balanced combination of mechanical, thermal, and dielectric properties, ensuring reliability in extreme conditions.
5. Applications of LCP Films
5.1 High-Frequency Circuit Boards
LCP films are widely used in high-frequency circuit boards due to their low dielectric constant and loss. They enable efficient signal transmission with minimal interference, making them essential for 5G communication systems and millimeter-wave devices.
5.2 Flexible Circuits
The flexibility and dimensional stability of LCP films make them ideal for flexible circuits in compact electronic devices. These circuits are used in wearables, medical devices, and advanced consumer electronics.
5.3 Precision Electronic Packaging
LCP films provide excellent barrier properties and dimensional stability, ensuring the protection of electronic components in high-performance packages. Their resistance to moisture and chemicals enhances the reliability of devices in harsh environments.
5.4 Aerospace and Automotive Electronics
LCP films are used in aerospace and automotive applications for their heat resistance and lightweight properties. They support advanced systems like radar, sensors, and communication devices, ensuring performance under extreme conditions.
6. Conclusion
LCP films are critical to advancing high-performance applications in modern electronics. Their unique combination of low dielectric constant, low water absorption, and exceptional mechanical properties makes them indispensable for high-frequency circuit boards, flexible circuits, and precision electronic packaging. As technology continues to evolve toward higher frequencies and greater miniaturization, LCP films will play a pivotal role in enabling these advancements.
Stanford Electronics is a trusted supplier of high-quality LCP films, supporting diverse applications with reliable material solutions. Visit our website for more information.