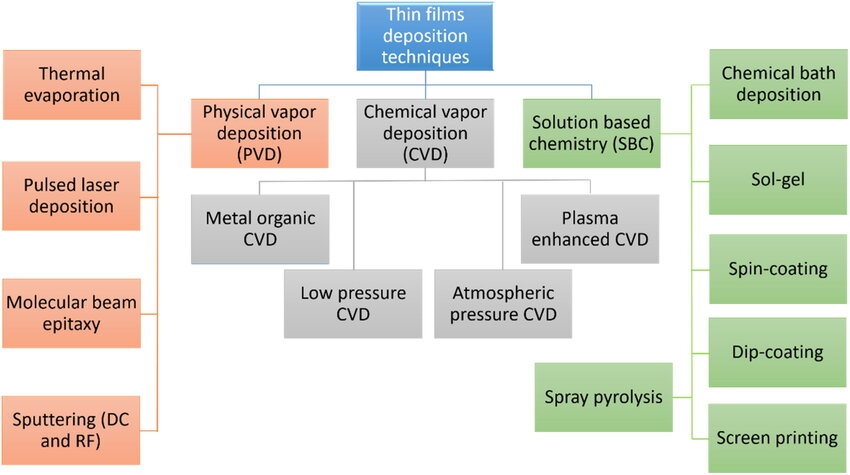
CVD vs. PVD A Comparison of Thin Film Deposition Techniques
Introduction
Thin film deposition plays a critical role in industries such as aerospace, electronics, medical devices, and tooling. Two widely used deposition techniques are Chemical Vapor Deposition (CVD) and Physical Vapor Deposition (PVD). Both methods enhance surface properties like hardness, wear resistance, and corrosion resistance. However, they differ in their processes, applications, advantages, and limitations.
This article explores the key differences between CVD and PVD, their working principles, advantages, disadvantages, and typical applications.
[1]
What is CVD (Chemical Vapor Deposition)?
Chemical Vapor Deposition (CVD) is a process in which a chemical reaction occurs on a substrate to create a thin film coating. This method typically involves heating a substrate in a reaction chamber while introducing gaseous precursors. These gases react at high temperatures, leading to the formation of a solid coating on the substrate surface.
Key Features of CVD
- Process Type: Chemical reaction-based deposition
- Temperature Range: 600°C – 1,100°C (1,112°F – 2,012°F)
- Coating Adhesion: Excellent due to strong chemical bonding
- Coating Uniformity: High, even on complex geometries
- Material Flexibility: Can deposit carbides, nitrides, oxides, and metals
Advantages of CVD
✔ Produces dense, high-purity coatings
✔ Strong chemical bonding ensures excellent adhesion
✔ Uniform coating thickness even on complex parts
✔ Suitable for high-temperature applications
Disadvantages of CVD
✖ Requires high processing temperatures, which can affect substrate properties
✖ Longer processing times compared to PVD
✖ Generates hazardous byproducts, requiring proper waste handling
Common Applications of CVD
Industry |
Common Applications |
Aerospace |
Protective coatings for turbine blades |
Semiconductor manufacturing |
|
Coatings for surgical instruments and implants |
|
Tooling |
Hard coatings for cutting tools and drills |
What is PVD (Physical Vapor Deposition)?
Physical Vapor Deposition (PVD) is a vacuum-based coating process that physically transfers material from a solid source to a substrate without chemical reactions. The source material is vaporized using high-energy methods such as sputtering or evaporation, and the vapor condenses onto the target surface to form a thin film.
Key Features of PVD
- Process Type: Physical material transfer (no chemical reaction)
- Temperature Range: 200°C – 500°C (392°F – 932°F)
- Coating Adhesion: Good, but lower than CVD in some cases
- Coating Uniformity: High for line-of-sight surfaces
- Material Flexibility: Deposits nitrides, carbides, oxides, and metals
Advantages of PVD
✔ Lower processing temperatures, making it suitable for heat-sensitive substrates
✔ Environmentally friendly (minimal hazardous waste)
✔ Can deposit thin, high-hardness coatings
✔ Faster process compared to CVD
Disadvantages of PVD
✖ Line-of-sight limitation can lead to uneven coatings on complex geometries
✖ Lower coating thickness compared to CVD
✖ Adhesion strength is not as strong as CVD
Common Applications of PVD
Industry |
Common Applications |
Decorative and wear-resistant coatings |
|
Medical |
Biocompatible coatings for implants |
Tooling |
Hard coatings for drills and dies |
Optics |
Anti-reflective and protective coatings |
CVD vs. PVD: A Direct Comparison
The table below highlights the main differences between CVD and PVD:
Feature |
CVD |
PVD |
Deposition Method |
Chemical reaction |
Physical material transfer |
Temperature Range |
600°C – 1,100°C (1,112°F – 2,012°F) |
200°C – 500°C (392°F – 932°F) |
Coating Adhesion |
Strong (chemical bonding) |
Good (physical bonding) |
Coating Thickness |
Thick (5-50 µm) |
Thin (0.5-5 µm) |
Coating Uniformity |
Excellent (even on complex shapes) |
High (limited to line-of-sight) |
Processing Speed |
Slower |
Faster |
Substrate Sensitivity |
Less suitable for heat-sensitive materials |
Suitable for heat-sensitive materials |
Waste & Environmental Impact |
Produces hazardous byproducts |
Eco-friendly (minimal waste) |
Which Process Should You Choose?
Choosing between CVD and PVD depends on the application’s specific needs:
· Choose CVD if you need:
- High adhesion strength and thicker coatings
- Excellent coating uniformity on complex parts
- Extreme wear resistance for high-temperature environments
· Choose PVD if you need:
- Lower processing temperatures for heat-sensitive materials
- Thinner coatings with high hardness
- Eco-friendly and faster processing
Conclusion
Both CVD and PVD offer unique advantages and are widely used for industrial coatings. While CVD provides thicker, more uniform coatings with stronger adhesion, PVD offers a faster, lower-temperature process that is more environmentally friendly. Understanding their differences allows engineers and manufacturers to select the best deposition method for their specific needs, ensuring optimal performance and durability in various applications. For more details, please check Stanford Electronics.
Reference:
[1] Pedanekar, Rupesh & Shaikh, Shahin & Rajpure, Keshav. (2020). Thin film photocatalysis for environmental remediation: A status review. Current Applied Physics. 20. 10.1016/j.cap.2020.04.006.